OCEANSIDE COMPATIBLE, BULLSEYE COMPATIBLE, 96 COE, 90 COE
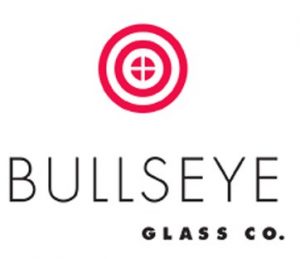





This type of work demanded more glass of consistent quality. 1851
Just look at their thumbs! They are lined with little cuts! Right! So annoying! Comes from pushing little pieces of glass against the grinding wheel. Unlike when we started out in business in 1988, now there is a gadget for everything
Did you know we do private parties at Stained Glass Express? These are plates that were made at a bridal shower! And a picture of the surprised bride.
Have no fear if you do not have a kiln, you can rent space in our kiln.
Step 1. Drink the wine! No problem with that step, right?
Step 2. Make sure the bottle is clean and dry inside and out.
Step 3. Apply Spray A to the side of the bottle that will facing up in the kiln. Be sure there is no spray A on the bottom as it won't burn off against the shelf. Spray A is very finely ground glass suspended in a medium that burns off clean. It not only helps prevent devitrification (a scummy layer that can appear on the glass after it is fired), but it will also help to keep any painted labels that may be on the bottle from burning off during the firing process.
Step 4. Use a kiln shelf that has been coated with kiln wash or covered with fiber paper. Leave enough room around each bottle to accommodate the spread as the bottles flatten out.
Step 5. Kilns are different, so make adjustments as necessary for your kiln. 300 DPH (degrees per hour) to 1100, then soak for 30 minutes (this allows the glass, shelf and air to reach equal temperatures) 400 DPH to 1450 soak for 10 minutes or until the bottle is flat. (take a peek)
Step 6. Cool AFAP (as fast as possible) to 1050 d. We don't suggest you open the lid because of the potential to thermal shock the glass. If your kiln doesn't have a controller, turn the power off until the temperature reaches 1050. Cooling quickly through the 1200 to 1350 range also helps to eliminate devitrification.
Step 7. Hold at 1050 for 1 hour and then cool 100 DPH to 400. the annealing temperature for bottles is somewhere between 1050-850 so you want to go slowly through this range. That's it. . . you have made a great gift! Add a cheese know tied with a piece of raffia to really kick it up! You can also paint with glass paint, use decals, sandblast designs--use your imagination! We will slump your bottle for you for $10. You must have it all prepared.