Stained Glass Express - The Blog / Category_Tips
Y96 Firing Schedule Guidelines
Please adjust hold times for the size of your project.
Remember, this is only a guide.
Full Fuse- From room temp to 1,000F at 300 degrees per hour, hold 10 minutes
- From 1,000F to 1,250F at 300 degrees per hour, hold 20 minutes
- From 1,250F to 1,425F at 300 degrees per hour, hold 15 minutes
- Crash from 1,425F to 950F, hold 60 minutes
- From 950F to 800F at 200 degrees per hour, hold 10 minutes
- From 800F to 150F at 300 degrees per hour
- Natural cooling to room temperature
- From room temp to 1,000F at 300 degrees per hour, hold 10 minutes
- From 1,000F to 1,250F at 300 degrees per hour, hold 20 minutes
- From 1,250F to 1,350F at 300 degrees per hour, hold 10 minutes
- From 1,350F to 950F AFAP, hold for 60 mins
- From 950F to 800F at 200 degrees per hour, hold 10 minutes
- From 800F to 150F at 300 degrees per hour
- Natural cooling to room temperature
- From room temp to 1,000F at 300 degrees per hour, hold 30 minutes
- From 1,000F to 1,225F at 200 degrees per hour, hold 10 minutes
- From 1,225F to 950F fairly quickly, hold for 60 mins
- From 950F to 800F at 200 degrees per hour, hold 30 minutes
- From 800F to 150F at 300 degrees per hour
- Natural cooling to room temperature
REQUIRES EYE CONTACT.
REMEMBER, THIS IS ONLY A GUIDE.
Wissmach Luminescent Glass
Luminescent glass is different than iridescent glass. It is low-fire—not high-fire like iridescent—and is intended for reverse fusing.
What is reverse fusing? Reverse fusing means placing your piece facedown on the kiln shelf and building backwards, fire-coated side down. If you are firing on a textured mold, place a piece of ThinFire between your boron-treated mold and the glass. If you fire your piece with the coated side up or cover it with another piece of glass, you will lose the coating. If you are slumping and do not go over 1,200 degrees, you can place the luminescent side up and not lose the coating. Luminescent glass is food-safe and has been tested by the U.S. Food and Drug Administration. However, please note that once the piece has been fired in your kiln, it is no longer a Wissmach product; it is your product. If you have been firing glass that could leave lead or cadmium traces in your kiln, that could get on the product, which would render it unsafe for serving food or beverages.
Firing Schedules: Courtesy of Petra Kaiser and Wissmach Glass
Standard Fusing Schedule – 2 Layers Thick
Segment 1: 600°F/hr up to 1,000°F, hold for 10 minutes
Segment 2: Full/9,999 up to 1,410°F, hold for 10 minutes
Segment 3: Full/9,999 down to 950°F, hold for 60 minutes
Segment 4: 100°F down to 700°F, hold for 1 minute
Tack Fuse, Polishing and/or Slumping into a Mold
Segment 1: 300°F/hr up to 1,000°F, hold for 10 minutes
Segment 2: Full/9,999 up to 1,300°F or 1,350°F (depending on your desired results), hold for 10 minutes
Segment 3: Full/9,999 down to 950°F, hold for 60 minutes
Segment 4: 100°F down to 700°F, hold for 1 minute
Draping over a Mold and/or Polishing
Segment 1: 300°F/hr up to 1,000°F, hold for 10 minutes Segment 2: Full/9,999 up to 1,200°F or 1,220°F (depending on your desired results), hold for 10 minutes Segment 3: Full/9,999 down to 950°F, hold for 60 minutes Segment 4: 100°F down to 700°F, hold for 1 minuteNOTE: Not all kilns are alike. Your kiln size, controller type and individual project may require some alteration to the schedule for best results.
Mind the Gap!
- Use push pins or jigs to hold your glass in place while building and checking the fit. That way, you won’t get one piece fitting perfectly as you are pushing another one out.
- Make sure you have not flipped any glass over. Label your pieces to avoid this.

STAINLESS STEEL MOLD PREP
- Cover with fiber paper or ZYP
- Spray with Boron Nitride (ZYP)
- If you use ZYP you rarely have to do it again
- I don’t use anything on stainless steel. As long as the glass is NOT an opal glass in contact with stainless steel and it is good quality, it is fine. You get a real shiny finish on the surface in contact with the stainless steel.
- It is minimal work to use a barrier. I would rather be sure instead of concerned.

Foils.. why so many?
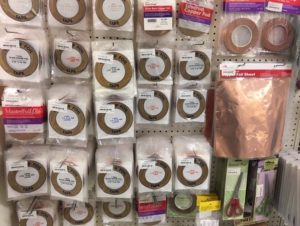


LITTLE HANGERS
When doing jewelry or small pieces there are several ways to hang. What you don’t want to do is ruin the looks! One of the cleanest looks is a jewelry bail which is glued on when the piece is out of the kiln. Available in different sizes, shapes and finishes.
https://www.stainedglassexpress.com/?target=search&mode=search&substring=bails&including=all
There is also a form of a bail that has prongs to go into a hole that you have prepared in your glass. You do this by drilling the hole after the glass comes out of the kiln.
https://www.stainedglassexpress.com/sterling-silver-leaf-prong-pendant-bail.html
Another option is high temp wire. This can go right into the kiln. Put it between two pieces of glass so it fuses and becomes part of the piece. This is available by the roll or in little preformed hangers. This does not stay shiny silver when it is fused. It darkens.
https://www.stainedglassexpress.com/?target=search&mode=search&substring=3210&including=all
https://www.stainedglassexpress.com/high-temp-wire-24-gauge-10-ft.html
Handy Hangers are made of brass, so they can go into the kiln. Put them between two pieces of glass. The same folks who manufacturer handy hangers just came out with the Finley hanger which is more delicate than the handy hanger.
https://www.stainedglassexpress.com/finley-fusible-hangers.html
https://www.stainedglassexpress.com/?target=search&mode=search&substring=207158&including=all
The other option which is a different great look is to put fiber paper as a spacer. Fiber paper comes in different thicknesses or you can stack it.
The Beginner’s Torch Trap: A Lampworking Torch Buyer’s Guide Part 1

EGGBEATER JESUS GLASS FALLING


WHICH SIDE IS THE COATED SIDE OF DICHROIC

HOW TO BUY A KILN
- How much space do you have
- Do you want to go to the expense of 220 line or get by with what you already have?
- Size of the kiln
- Programming




Tips From the Glass Academy: DECALS—TIPS AND TRICKS For applying to Dichroic Glass
